The Tata Steel Group is among the top global steel companies with an annual crude steel capacity of 27.5 million tonnes per annum (MTPA). It is a geographically-diversified steel producer, with operations in 26 countries and a commercial presence in over 50 countries.
The Group recorded a consolidated turnover of US $18.12 billion (INR 117,420 crore) in FY17. Tata Steel Group is spread across five continents with an employee base of nearly 70,000 employees, as of March 31, 2017.
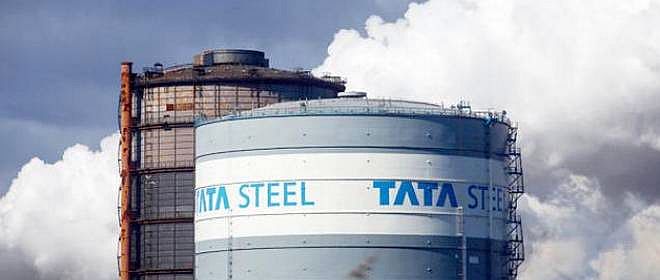
Tata Steel cooling towers
The Group uses as many as 200 cooling towers (CTs) at its plants across the world. These are medium and high capacity CTs with capacities as high as 1,000 TR (Tons of Refrigeration). The CTs consume a very high amount of energy, significantly increasing the operational costs of the plants. Tata Steel was looking for a way to improve the efficiency of the CTs, to reduce energy consumption and save costs.
“The CTs can only be modified through retrofitting. Improving their efficiency through software algorithms is a better and more cost-effective approach,” said Dr Supriya Sarkar, Head, Environmental Research Group, Research and Development and Scientific Services, Tata Steel Ltd. “With just a software change you can achieve a 40% efficiency improvement.”
Tata Steel wanted to implement a control strategy so that the cooling tower can be operated in a more efficient way. Heavy duty CTs are attached with blast furnaces, while medium rate CTs are attached with HVAC systems and process chillers. There are two energy-intensive components in the CT: the pump and the CT fan. These components are driven by heavy-duty motors, which consume a lot of energy.
“If we can reduce the energy consumption of the pump and the cooling fan, then energy will be saved significantly. To do that, we have to install the VFD (Variable Frequency Drive) instead of the control valve. VFD is the final control element,” informed Dr Sarkar.
There are control algorithms and process algorithms that determine the operation of the VFD controller. These algorithms are developed by MathWorks.
MathWorks provides the modelling approach and the control development approach. For the modelling approach, Tata Steel developed some optimisation algorithms based on first principal laws. Over time, it will tune the performance of the VFD controller, as per the plant data.
To do that, a digital twin model of VFD controller was created. The digital model is continuously updated based on data from the real world or the actual plant. This improves the accuracy of the model. When the model is accurate it is easier to make physical controller (VFD) more efficient.
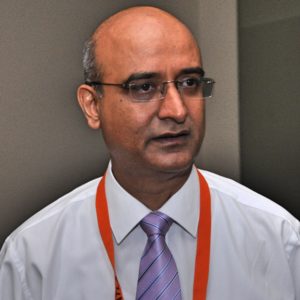
Sunil Motwani, Industry Director, MathWorks India
“This is like adaptive control and optimisation, being done together,” said Sunil Motwani, Industry Director, MathWorks India. “The model parameter is getting adapted. So, it is an adaptive model of the plant and the adaptation is done based on the plant information or real-time data or actual data coming from the real plant.”
This is based on first principle modelling, which uses physics equations, which is theoretical.
“To that theoretical model, they are feeding in real data coming in from a real system. This makes the model more realistic – it becomes a digital twin of the real operating system. If the model of a physical system is very accurate then it is easier to make the controller more efficient. A first principal model does not accurately represent a real-world operating system. It is theoretical. There could be many more things happening in the real-world,” informed Motwani.
The entire program was developed in MATLAB. The development team used the MATLAB compiler and Simulink – simulation and model-based design. There is a standard built-in package of Optimizer, a MATLAB optimisation toolbox. LSQ non-linear squares and control system toolbox was also used.
After successfully improving the accuracy of the model, Tata Steel can now attempt to make the VFD controller more efficient.
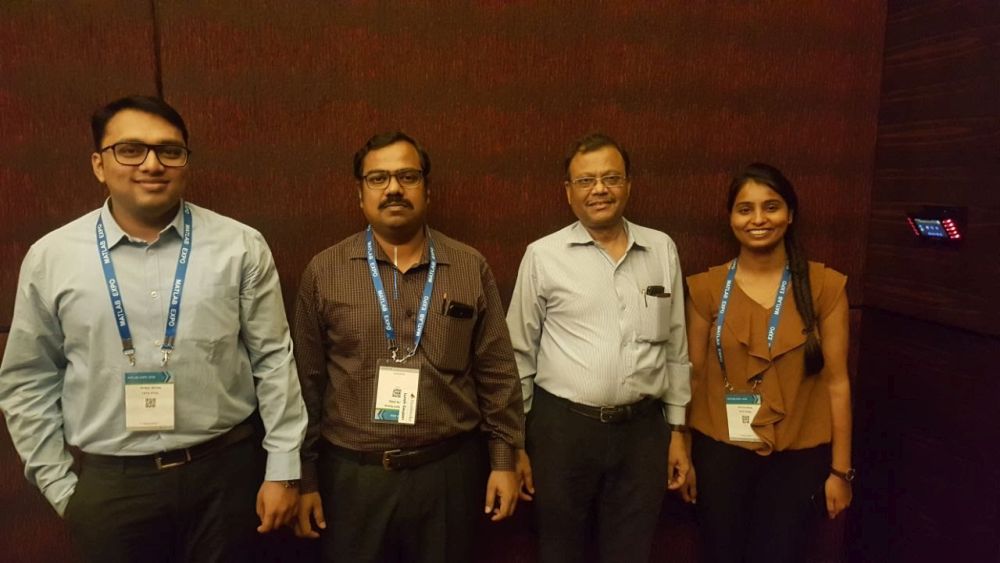
The Tata Steel Environmental Research Group team
“We have optimised the process. The tonnage of a certain CT is 1200 TR and it consumes almost 2 MW power (2,000 KW). We took the data from the CT, implemented our control algorithms and derived a simulated result. We found the 40% energy can be saved without hampering many things. It was a simulation model, a digital twin,” said Dr Sarkar.
Dr Sarkar and his team are now talking to the plant team to implement the changes in the physical VFD controller. They will implement a pilot plan, a proof of concept, done on a smaller scale.
“The pilot plan will have all data capturing facilities and we will connect it with iMonitor or Historian (Data Analysis). It will collect all information and feed it to the MATLAB algorithms,” informed Dr Sarkar.
But making cooling towers more efficient through algorithms and modelling techniques is only one aspect of digitisation for Tata Steel.
“Apart from CTs, there is a need for using these algorithms in many other areas within the organisation for digitalisation. Accenture is helping Tata Steel with Digital Value Acceleration. These initiatives will explore core areas for the implementation of AI and machine learning,” said Dr Sarkar.
This is a good example of how domain experts from the industry (with some knowledge of data science) can use simulation and modelling techniques and algorithms to improve efficiencies.
“Our tools help domain experts (in the industry) adopt data science or digitalisation to add value to their process. You don’t need to be a data science expert to use our tools,” concluded Motwani. “Tata Steel engineers from different domains (chemical engineers, biotechnology engineers etc) simulate the processes in small pilot plans, analyse data and then scale up. They come together and use our tools and data science as a technology to bring in more efficiency in their systems.
Related story: How Engineers and Domain Specialists are Pursuing Data Analytics